There are many different types of track surfacing on the market for every budget and use. Which is right for you?
Throw in colors, configurations, top coatings and markings, and the possibilities are endless – if not overwhelming. Understanding the difference between a polyurethane track or Mondo or latex is crucial to understanding what your school needs.
Polyurethane tracks make up the overwhelming majority of tracks installed at both high schools/middle schools and colleges, particularly in the Northeast. There are many different types and systems in polyurethane, but the basic principle is that the track is the result of a chemical process, mixed and installed on-site.
Polyurethane tracks have elasticity, meaning they can withstand harsh winter freeze/thaw cycles. Depending on the specific system, polyurethane tracks can routinely last over 10 years before a simple, economical resurface is needed.
It’s common for the asphalt base beneath a polyurethane track to last upwards of 25 years and need one resurface in that time. Certain polyurethane tracks (“mat and spray” tracks) can be resurfaced more often in that lifespan but cost less at the outset.
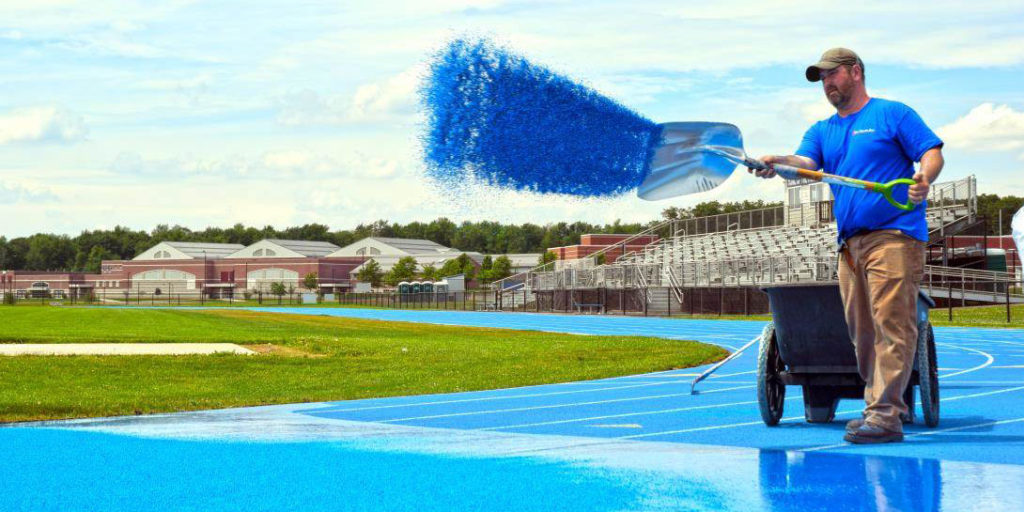
When a polyurethane track wears over time, it maintains its usefulness. Outside damage caused by outside forces, these tracks rarely wear away to leave dangerous cracks and divots in the surface, even at advanced ages. There are also few seams, limited to just three or four areas, typically, which are carefully addressed during the install process to assure they don’t come apart.
Polyurethane tracks use EPDM rubber to create a top course that retains its texture over time. The materials used are designed to be comfortable to run on without sacrificing the speed of the athlete running on it – regardless of the age of the track.
The balance stuck between quality, longevity and cost are what polyurethane tracks by far the most popular choice.
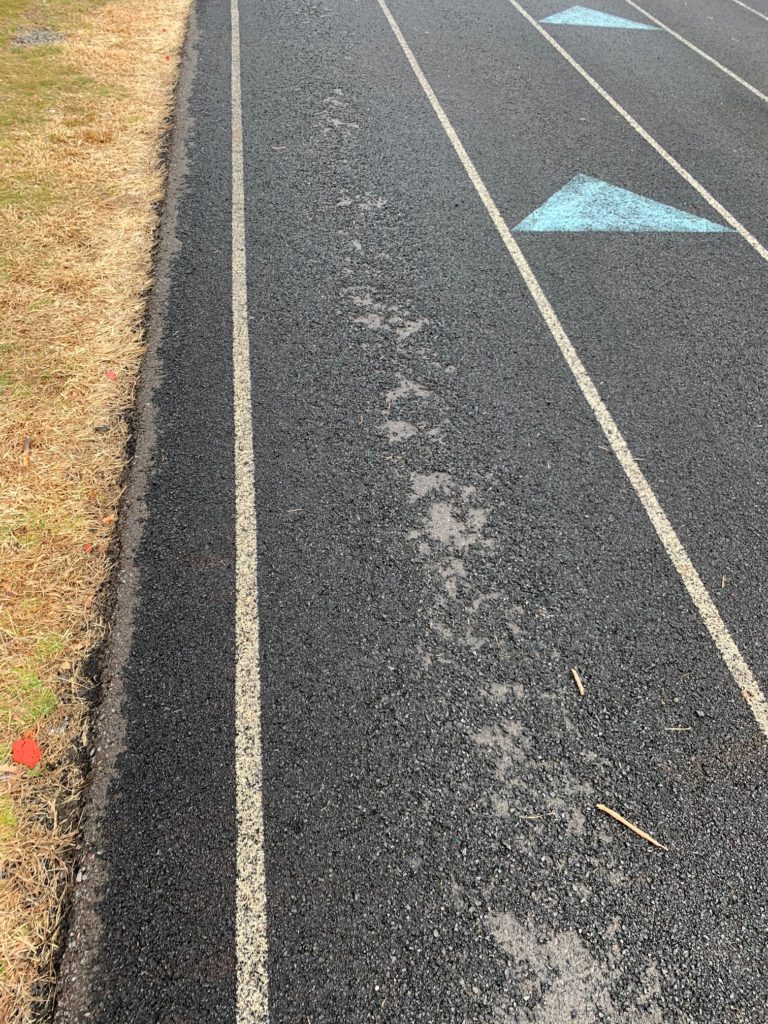
Latex tracks come in at a lower cost, but should be resurfaced more often than polyurethane surfaces. These tracks also lack the “give” of polyurethane tracks. When they wear, they can become brittle and crack, but also wear away, breaking apart and exposing the asphalt base.
Latex tracks work for owners on the tightest budget, but long-term costs and maintenance are higher.
Mondo is the surfacing used in the Olympics. It comes in at the highest cost and it’s a prefabricated, rolled material that’s manufactured, delivered to the site and glued into place.
Most Mondo surfaces are said to be 10-year solutions. Mondo’s installation methods mean the track is covered with seams, both where lanes meet and at the end of each rolled section.
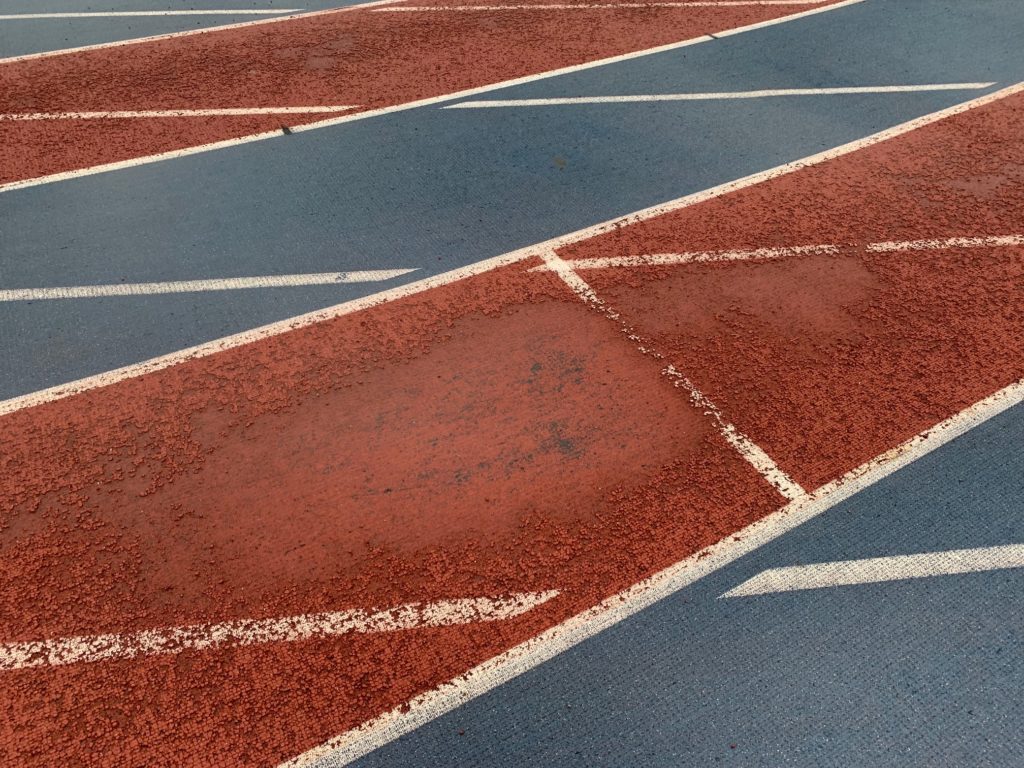
Mondo surfaces need to be removed and replaced when they have come the end of their useful life. Unlike polyurethane or latex tracks, a new surface can’t be simply installed over the existing track (with the exception of installing a new polyurethane top). Depending on the age and environmental factors, the asphalt below the Mondo surface needs to be repaired or replaced after the surfacing is removed.
The firm top of a Mondo track is part of what makes it “fast” but they can also show significant wear in high-traffic areas over time. The surfacing also tends to “crumble” as it ages and the top layer is worn off.
People can debate the speed of different track surfaces all day, but there is clear delineation between each of the three predominant types of surfacing out there today. Properly maintained, polyurethane tracks last longer and cost significantly less over decades, but carry a higher initial cost than latex and Mondo can boast its use on the international circuit.